Update
We had to withdraw the DuckyPoxy from the market while we worked out some problems. It turns out that the ratios for the accelerator will adversly affect the strength of the epoxy when added at more than 10%. So we will be adding a faster speed hardener soon. In the meantime, we have had requests for the slow version so we are making that available now.
Background
I have been exposed to wood working and working with wood in different ways for most of my life. When I was growing up, my father, a university administrator, had a double garage full of power tools and built a houseful of furniture and at one point a 22 foot cabin cruiser. Shortly after Sandra and I were married, I partnered up with a couple of fellows who were falling timber in Montana. This business grew into a sawmill, which I ran until it morphed into a forklift pallet manufacturing business.
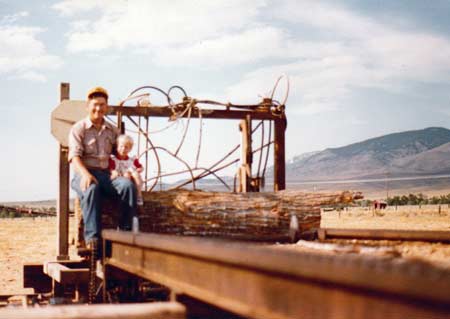
Sawmilling in Montana
Soon afterward, we returned to Texas with our first two kids, and I got a job as an apprentice patternmaker. Few people know what a patternmaker is – I didn't when I took the job. In simple terms a patternmaker is a craftsman who takes engineering drawings and renders objects in three dimensions. Most often these renderings are in wood. Nowadays we just turn on a 3D printer but this was way back in the last century.
Most of the objects that patternmakers make are tools to be used for the production of sand castings in aluminum, brass, bronze, iron, steel, etc., and they tend to be industrial: valve bodies, gears, housings and other uninspired shapes. To suck even more soul out of the job, all dimensions are to be held to 10/1000ths of an inch or less tolerance. This is woodworking we are talking about.
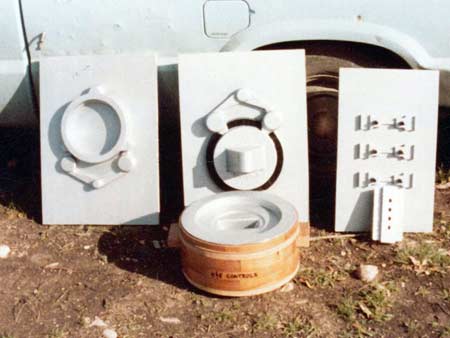
a few of the patterns I made back in the day
Don't get me wrong, I liked the job in general. The pay was good and every job was new and different. But soon after starting down this career path, I began building boats. What a relief it was to tell if a shape was right merely by standing back and looking (using what John Welsford refers to as my "eyechrometer") rather than measuring with precision steel rulers from three different datum lines.
My first boat building project was a pair of 8 foot prams to use teaching my kids to sail. That was my introduction to stitch and glue. With this system, any idiot could make a joint at any angle that was stronger than the plywood on each side. The joint could even change angles throughout its length. It was like magic. Fast, strong, light - What a revelation! 30 odd boats later, I am still still learning about this amazing polymer.
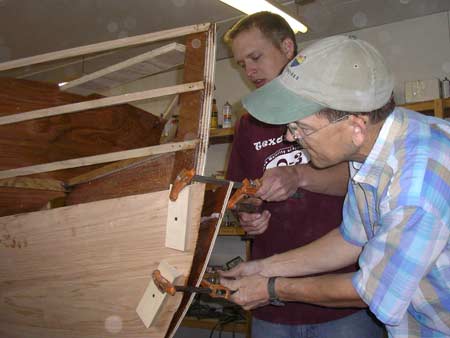
One of the boats along the way
I probably used West System epoxy back then as that was about all there was. Since then I have built over 30 boats from a Bolger Tennessee to a PDRacer or two. I have built sailboats, powerboats, rowboats and paddle boats. I have used different types of goo too, Titebond, PL Premium and even Gorilla Glue. I have found that each has its place but epoxy can do the most, especially if an attractive finish is desired.
Back when I started there were 5 basic problems with epoxy:
- It would often blush, causing extra work to remove that waxy surface residue.
- It would overheat (become exothermic) to the point of smoke or even flames if not applied quickly enough
- The hardener that causes the resin to cure comes in usually 3 fixed speeds which limit a builder to certain shop temperatures.
- it would degrade quickly when exposed to UV light
- it contained Bisphenol A (BPA), a potentially dangerous chemical which has been banned from many consumer products.
Since that first project, I have used many different brands of epoxy and most of the newer formulations are "blush free" – a big improvement – so problem #1 sorted. But the other four issues have remained – until now.
Enter ResTech
In April, 2015, I got a phone call from Scott Phillips of ResTech, an industrial epoxy formulator. He told me a little about their new Novolac BPA-free epoxies and offered to produce a Duckworks branded product for us. I agreed to try a sample. I was encouraged that this epoxy not only did not have any of the nasty Bisphenol A, but also contained two different UV inhibitors. In addition, he claimed it would not go exothermic. So, with the first sample, I mixed a 9 ounce batch – this is a lot for Texas in April. The first thing I noticed was that the stuff actually smells pretty good. I grabbed a scrap of plywood and coated one half with the ResTech product and the other half with some standard boat building epoxy. I put the piece out where it would be in the sun every day – the ResTech side is still good 6 months later – a good start. The other side is visibly yellow and cracking as I knew it would.
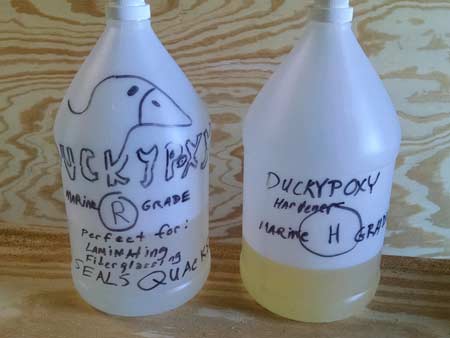
One of the many samples from ResTech - you can't
tell me these guys don't have a sense of humor.
But back to that big batch of resin/hardener mix: I kept feeling the container and waiting for it to heat up. The temperature in my shop that day was about 75⁰F so I expected the batch to be hot after half an hour. An hour later it was barely warm. It took two full hours to cure. I could see this was a blessing and a curse. On the one hand, beginners who often have trouble with exothermic reactions would benefit greatly, as would anyone working in a hot shop, but someone working in a cool climate or wanting to get a cure quickly and move on would be out of luck. Overall, I was encouraged.
We drove up to Dallas to talk to Scott and his technical folks. We had a few issues. First of all, the resin in the sample was almost too thick to pump with a standard mustard pump. No problem, Scott's tech, Whitney, would fix that. Then there was the speed problem. I explained to the guys that boat builders need different speeds of epoxy for different temperature conditions and for different jobs. Filleting, for instance, is slow work and wood flour somehow exacerbates the exothermic reaction – for that you want a lot of working time. But when glassing the bottom of a boat, you mix and pour relative quickly so a much faster cure is wanted.
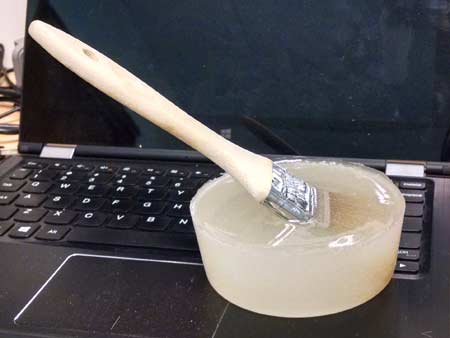
I mixed this batch of over 8 ounces of epoxy in a plastic cup on a warm day and let it sit. Any other epoxy would have heated up and melted the cup resulting in a huge mess.
Whitney, being familiar with resins and their formulations, quickly offered that they could easily produce different speeds of hardener. All that would be needed was a bit of tweaking to the formula. Then Scott, who had been listening quietly to all this, offered what can only come from someone not familiar with a process but who sees it from a fresh point of view:
"Why not offer the customer one basic speed of hardener and a small bottle of accelerator to make it cure at whatever speed they need at that moment?"
It was brilliant! In my shop, I have three different speeds of hardener, fast, slow, and tropical. I keep those because I am a serial boat builder and buy epoxy when I need it as I know I will always build another boat. Since the shelf life for epoxy is almost forever, I will eventually use it up. But what about a beginner who is not hooked yet and thinks he will only build one boat. The smallest bottle you can get epoxy in readily is a quart, making a three quart kit about the least you can buy, and it is only going to have a single speed of hardener. Add to that kit a little bottle of accelerator - Problem solved.
We left Dallas with a fresh gallon and a half of epoxy and a bottle of accelerator. On the drive home that day, Sandra and I pretty much made the decision to take the plunge and get into the epoxy business. This stuff being all new with the UV inhibitors, the very slow cure option, the variable speed, and the Novolac formula, I wanted to call it "Epoxy 2.0". Sandra gave that the thumbs down. She liked "DuckyPoxy" and that is what we called it.
The first thing I did when I got back to the shop was a series of tests using some RAKA Tropical speed and Marinepoxy with both slow and fast hardener against several different batches of the sample epoxy with differing small amounts of accelerator. What I found was that I could indeed get different cure speeds with the accelerator. I could match any of the cure speeds of the regular epoxy by adding predictable amounts of accelerator. I had satisfied myself that this was all a good idea. We made up labels for our new epoxy and at the recommendation of Bill Moffitt, called the accelerator "Goose-it".
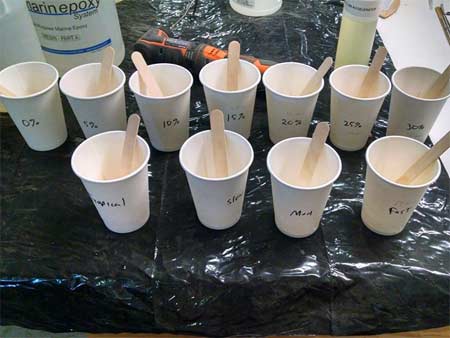
I ran a lot of tests to gauge DuckyPoxy cure rates
against other popular boat building epoxies
So now we are ready to go. If you would like to try a small sample batch of this stuff, let me know. You can find it in our store here:
https://www.duckworksbbs.com/supplies/epoxy/duckypoxy/
You don't need to thank me for bringing this wonderful new product to market – your business will be thanks enough.
Chuck Leinweber
Duckworks Boat Builder's Supply
|