Building a Light Schooner in Winter
by Rob Rohde-Szudy
Hey
Folks
I'm building a Bolger Light Schooner up here
in Wisconsin. You might recognize my name, as I've written a couple
articles on Jim Michalak's site about the building of my Piccup
Pram.
Thought you might be interested in how I'm getting
all this done in the winter up here. PL400 helps, since it cures
at 10 degrees F. But notice the "painting booth". My
dad's shop is 14' tall - way to high a ceiling to keep any heat
in. And it is attached to a 2 car garage with no wall in between.
Same deal.
So I put some screw hooks in the walls every
4' about 10' above the floor. Then I screwed some pairs of sheetrock
screws into the wall at convenient spots - these to use as cleats
for mason's twine. The roof of the booth is cheap (scrap actually)
styrofoam beadboard sheets. I drilled a hole at each corner with
a 3/8" bit. With beadboard you have to run the drill in and
out a few times to clear all those clingy beads.
Then I cut a length of mason's twine for each
screwhook, running floor to hook to floor, roughly. I also cut
some 5-6' lengths of twine and tied them into loops. A true lover's
knot works well. The other thing needed is some longish, thinnish,
narrowish scraps of wood.
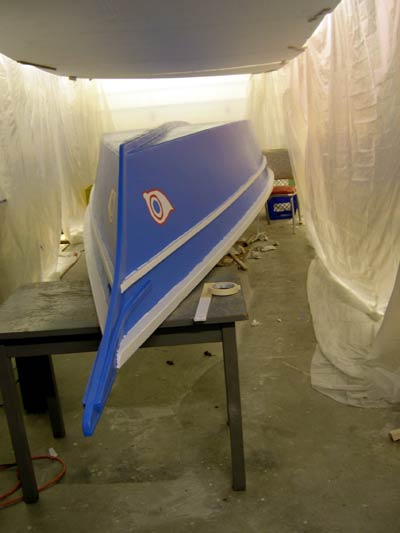
The loops are held double, like a string, and
run through a beadboard corner hole AND the corner hole of the
adjoining sheet. The easiest way to get them through the beadboard
is to blow the loop through the hole. Then I ran the narrow wood
scrap through the loop so it can't come back through. Duct tape
helped keep it in place until hoisted, and the scrap wood is what
actually carries the (small) weight of the foam.
It helped tremendously to have a partner in
this job, one person on each side. Once each loop was fastened,
we tied to it the twine running up to the screwhook. Then hoisted
and cleated to a pair of screws.
Of course this is only a roof, so far. For the
walls, clear plastic sheeting is an obvious choice, since it lets
light in and is cheap. Most would try to duct tape the plastic
to the top of the foam, but I knew it would let go in the cold.
I had a can of old, rusty 16d nails that I was unlikely to ever
use on anything I cared about. So they became spikes. I rolled
a "hem" of 3-4 turns on the upper edge, pinning through
it into the top of the foam every 18" or so. It has worked
like a charm with no sign of letting go. I pulled out a nail or
two by standing on the plastic in ways I shouldn't have, but the
nails are so easily reset that I can't complain about it.
In weather in the 20s and 30s I only need one
heater of 2500 watts to stay over 50 degrees. Colder than that
and I have to add another of 1500 watts. But that's for a 24'
boat AND about a 12x12 attached shop area, so I think most projects
would do fine with much less. When building the Piccup, for example,
I was able to use PVC pipe arches with plastic sheeting, and the
small heater was more than enough.
Best of luck to fellow winter builders!
Rob Rohde-Szudy
robrohdeszudy@netzero.net
PS: Please have a look
at the "messabouts and events"
link in the upper left corner of any duckworks page. This is
where you find out about all the get-together opportunities
for the coming season! - Rob
|