Clinker built boats are, coming
back strong. To meet the resurgence
toward clinker construction I have
designed Kingfisher. She is 17 ft.
overall, and is therefore the smallest
of similar inboard powered, craft.
She comes between the point where
the 15-footers of outboard flash leave
off and the 18 and 19 and 20-footers
of inboard persuasion begin. She has
6'6" of beam, weighs near 1,300 Ibs.
ready to launch, and so will haul and
trail easily.
She is a high-sided little mite,
havings 34" freeboard at the stemhead and 27-1/2" freeboard at the
transom. This makes her proportionately deeper but that, too, is a good
thing: wind will bother her passengers less, and since' she has "good
long legs" in her lateral plane, cross
winds won't knock her about.
Her deep entering forefoot helps
in that regard. A slight hollow to the
water lines results, which purls the
bow wave under in pretty fashion. I
have built a model and tested it, and
Kingfisher will prove very free running.
In fact, she can be very adequately
powered with either of the two
smallest inboard marine engines on
the market. The Brennan Imp made
by the Brennan Motor Company of Syracuse, New York, or the Universal Atomic Four made by the Universal Motor Company of Oshkosh,
Wisconsin, will prove very satisfying for power.
The Brennan Imp will push the
boat 12 to 14 miles an hour. The
slightly larger Universal Atomic
Four of 25 hp will give you 14 to 15
miles as will a Gray Seascout or a
Kermath Sea Cub.

For those who want real "rush", a
Gray Lugger of 33 hp Will give 17 to
18 miles, and any of the 60 hp 133
cu. in. kit boat motors like the Gray,
or Chris Craft "B" (built around a
Hercules block) or the Universal
Unimite will giye 22 miles.
More power will Just be wasted.
To anticipate the inevitable—yes,she can also be built as an outboard by the simple expedient of cutting away the trailing skeg, framing the transom to suit a motor opening. A 25 hp outboard would "poosh" her 16 to 18 miles an hour light.
Lest some who have a bit of know-how, but little know-why, accuse me of imitating anything like the Lyman Islander or similar craft, such as the Century or the Cruisalong as the Century Buccaneer, let me call to the attention of such that it was 24 years ago in Motor Boating that the plans for Kidette appeared. This was a 17-footer of my design which had wide beam, clinker topsides, a 32 hp light
motor, and exactly the same cockpit layout as today's most imitated boats.
I am not Suggesting that today's designers of the highly popular clinker utilities ever saw the plans of Kidette. What I am pointing out to your up-raised eyebrow, is that Kidette, placed alongside the most
imitated boat of today would show the same general characteristics, and would cop the First-of-Type Trophy.
Kingfisher is small enough to be squeezed into the average garage when building. Please realize that any home-built boat involves three steps before you are even Stephen with the professional shops: You must have a good bench, good tools, a dry place to work. Also you must make out a bill of materials and get your lumber on hand. Next you must lay the boat down full size—all of
it—profile, half-breadths and body plan, and fair it. Then you are on
the line, on the mark, and can proceed with no more than average troubles.
Kingfisher will build easily. Any
pro boat builder who knows his trade
will tell you that the boat which is
built of light material in small parts
will go together easier than the big
hunk stuff. It may take longer, but it
is easier.
Let us assume you are about to
forsake being a dreamer about this
boat and plan to become a doer. The
first thing to do is to get one more
copy of this Boatbuilding Annual so
you'll have a clean, and clear, reference to work from. One copy will become smeared, smudged, illegible.
Get one before the next guy has the
same idea.
Next, send to Motor Boating, 572
Madison Avenue, New York, New
York, for Vol. 34, Practical Boatbuilding. This is a recently reprinted
volume, containing the priceless
boatbuilding lore of H. W. Patterson, formerly chief designer with
Consolidated Shipbuilding Corp.,
"New York and a most thorough and knowing constructor. There you will
find spiling method, layout, fastening methods—everything you might
be groping for and which would be
impossible to give here in limited
space. The price is $4 postpaid.
Next get a roll of brown paper,
some battens, nails and weights, and
now follow my constructional specifications.
Lay the job down full size, fairing
out obvious errors and little errors
in the offset table as you go.
Next make the moulds. These can
be of scab lumber. They must diminish by one thickness of planking
from the faired-up body plan. The
laps compensate each other and this
reduction in skin size gives proper
designed displacement.
Erect the moulds on a grid marked
on the floor as shown in the perspective drawing. The braces you will
use are not drawn in.
As shown at "A" on the perspective sketch, most pro boatbuilders
would diminish the moulds by one
planking thickness, and plank before
framing. It would be much easier for
the home boatbuilder, though, to diminish the moulds by the thickness
of one plank, also of one frame and
one ribband. Built thus, the frames
can be bent (after steaming) about
the ribbands, and the planking can
be spiled directly from, and applied
to the frames by one man working
alone. More, he can quit when he
feels like it, with each plank properly nailed. And he can rivet each
lap to each frame working alone.
More initial trouble, less final trouble, a fairer hull.
The stem is of oak, sided 2-5/8" and
moulded as per plan. The knee is
the same. The cark can be of tamarack, or yellow pine. ("Cark" means
core or burden, hence load earner,)
This assembly bolts as shown to the
keel and apron. The keel may be of
2-5/8" sided white oak, or 3" fir or
yellow pine. The apron is of yellow
pine, 1-1/2" x 5".
Abaft the drop in the keel where
it leaves the apron, a filler is laid to
form a rabbet edge for the aft run
of the garboard strake.
The frames are of oak, 11/16" x 1-1/16"
on 6" centers. The heels of each
frame are boxed neatly into the apron, screw fastened. The frames
are chamfered or rounded on the inboard edges. They are steam-bent,
which is a great labor saver in boatbuilding, and should frighten only
those who have ever had trouble
boiling oatmeal or cooking an egg in
hot water.
Sooner or later you'll run into the
seeming conflict in frame sizes. The
lines call for 7/8" x 5/8", the inboard
construction calls for 11/16"x 1-1/16'.
Use the lighter frame for an outboard motored hull, the heavier
frame for an inboard job. In each
case use the forward mark on the
lines plan for the 6" spacing.
Practical Boatbuilding, previously
mentioned, tells all about steaming
and gives plans for a $5 rig.
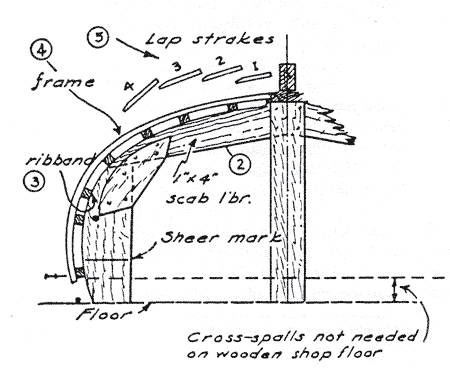
There are 14 strakes of planking
each side of the keel. Make the garboard and broad as dimensioned on
the scantling section. Then "line off"
a few battens from the sheer toward
the turn of the bilge. This means to
get a fair sweep to the few topmost
strakes. Spile the others between the
lined-off topmost strakes as planned
and the broad. If you spile all
the strakes, especially the topside
strakes, in a clinker job the run of
planking will seem to bend downward.
Philippine mahogany planking, of
7/16" finish, is best and probably
cheapest. Plywood, if of 5-ply special panel length, will be okay, but as
plywood by the board foot usually
costs just double untouched prime
lumber, why use it? That is for factories which have resaw rollers and
big tables.
Fastenings for the planking will be
copper clout nails, properly turned
with a clinch iron and set up with a
nail set about 1/16" to 3/32" into the planking. Any over-zeaious hammer
marks can be worked flush by daubing with water. This swells the wood
out again.
The transom construction, the installation of the risers and the engine
beds and bilge stringers are just simple, straightforward carpentry and
need little explanation. Before I go
along, the clout nails should be I-1/8"
long, and the double-lap rivet at
each frame (over a bur) should be
2" No. 12 nipped off.
I should judge all materials would
cost $400 and the motor will cost
what you select. Labor: between
300 and 500 man-hours. She'll build
in spare time over a winter.
WESTON FARMER