With most things in life, give ten people the same job to do and all ten will probably do it in a different way. One could call this natural ‘perversity’ (or if being kindly disposed ‘diversity’). Turning the hull of a boat over is no different, I have seen it done at least six ways on the internet, but none of them seemed exactly applicable to my task, in size, shape or location. So the only solution was to devise my own method. Hopefully, with a bit of huffing and puffing and some sweat, I can get the boat suspended over that nice new aluminium trailer I have just built. As usual it will have to be a one man job method, as being anti-social I don’t have any friends (no just kidding, I do have one friend, but usually work alone – only one person to get injured that way and I can work at my own pace).
Some of the possible methods are:
- Get about 15 hefty men, many crates of beer, one barbeque and a several bales of hay. First get your helpers thoroughly drunk – but not enough that they can’t stand up. Arrange them in two teams – either side of the boat, then try to get them to work in unison to turn the hull over. Stand well back to supervise, so you don’t get injured or squashed.
- Hire a crane to lift the boat on slings, not quite sure how it gets turned over but presumable the crane driver knows what to do.
- For a long time I favoured this idea, but what happens if you get a crane driver who doesn’t know what to do? In my case I don’t know what to do, as my trailer only has a keel bunk at present and I am not willing to pay for driver and crane for several days while I design and fix the other bunks to fit the suspended boat.
- Build a cradle round the boat with a circular outside profile and roll the boat over. Well to start with it’s going to have to be very solid as I recon the hull must weigh near a ton already. Even if I managed to build the cradle I don’t have the space to roll the hull as my boatshed has concreted-in posts which I want to keep for a while, and if I did manage to turn the hull how do I get the trailer underneath – another major job?
- Weld together two pivot brackets, one for each end of the hull. Sound quite good but I feel it would work better on a boat that has a vertical stem – unlike my own. Again another job for a welder and what happens when one bracket breaks or bends.
- Fix a couple of hoists to the ceiling and suspend the hull while you ease it round, then lower it onto the trailer. Sounds good but I don’t have a ceiling – or at least not one that would take more than 5% of the weight of the boat.
- Lever the boat over with long levers, rope and straw bales. A bit dubious if you are not 9’ tall and built like the Hercules.
One of these splendid ideas has to work for me, but which one?
In the end I decided that option 5 had most promise, the only problem was that I had no ceiling and no hoists, but not to be deterred by minor obstacles I set to and devised a method to get the job done.
The boat shed would have to be strengthened to take the weight, I may not be very bright with the welding but wood I do understand and being trained as a software engineer helps to organise and schedule the solution. Firstly, the polythene roof will need to be rolled back at the ends, or taken off to avoid damage. I can put it back on later, when the job is done, for the next phase of boatbuilding, till the wheelhouse gets too tall and I have to make adjustments. The next question I think should be. How can I lift the boat’s weight and turn the hull?
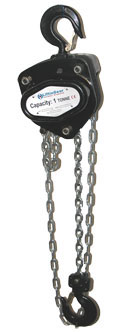
Does Not Enlarge
|
I found this little beauty on the internet. A one ton chain hoist with a 3 metre lift for £49 + VAT. As the boat weighs an estimate of under a ton, one of these each end should just do the job, and afterwards I can use it for other jobs like hoisting the engine aboard. A few pounds extra will buy a couple of 2 ton polyester lifting strops which I can wrap under the hull and later use to fasten the boat on the trailer for towing, the extra wood will be used for bunks and guide posts on the trailer. |
Now what do I fasten it to? Considering the boat shed as it stands, if I lengthen the uprights and put weight on them one of several things may happen:
- They may bend forwards/backwards and snap;
- The upright poles may not take the weight and buckle;
- The cross piece may not take the weight and may buckle;
- They may bend sideways and snap.
The first two problem are easy to tackle, I need to link the poles holding the cross piece to the ones in front and behind so a simple piece of wood bolted across all three, ideally a couple of pieces reaching up to the top of the extended centre piece will stop the join buckling.
To stop the cross piece from breaking it will need to be extra wide, 8” x 2” should be OK and if I double the thickness with two pieces of wood even better. But it is still a long way at 4.107 metres (about 13’ 6” for the non-metric people), so I plan to also support the cross piece closer to the centre. It will also help to have the lifting strop attached from these points rather than centrally.
As a picture always explains things more clearly, see below diagrams below
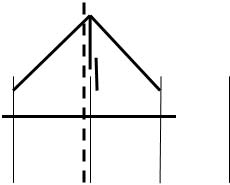
Does Not Enlarge |
Side view, the new pieces of wood are shown thicker with the existing uprights thin. Hopefully this will extend the support posts to the required height and brace them sufficiently. Note: As the central upright will be extended, another post will need to be bolted to it to hold the extension in place and strengthen it against the load. |
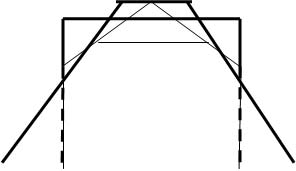
Does Not Enlarge |
The existing A roof support may be removed so that it does not interfere with the new structure. The angled braces will prevent the structure buckling sideways and will support the cross piece where it is loaded. The short extra piece on top, parallel to the load bearer will also prevent buckling. Note the second upright post is shown as a dashed line behind the current post |
Well that is the structure designed, now what about turning technique. First job will be to detach the boat from its building frame and to place a strengthening support across the hull where the strops will lie, I intend that the strops will sit next to frames, so a cross piece will be needed to brace the two frames. The slings are intended to hold a load and not allow it to slip, so I will need to wrap them with several layers of thick polythene sheet to reduce the friction. By raising the hull on one side (where the chain hoists are situated) and then fastening the side in place while releasing the hoist, this should cause the other side of the hull to tip. Repeating this process several times should result in the hull turning over eventually. So much for the theory!
Here is how it worked in practice
First let’s take a look at the practicalities of the problem. As you can see there is plenty of horizontal room in the shed, but not so much vertical room, I had to relocate some of the roof cross braces to allow more space. Getting the trailer out of the place where I had temporarily placed it took a bit of hard work as I couldn’t get the car coupled up. In the end I attached a rope to the car tow hitch. Almost every job can be done alone, it just takes more of everything – time, effort, ingenuity, and of course more scope for things to go wrong.
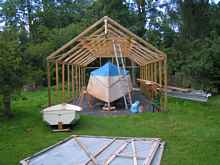 |
Strange how it is always quicker to pull something apart than build it. So far so good, the boat shed is stripped ready for action. |
Here is how the reinforcement worked out in practice, it helped considerably to draft out the solution to scale on a sheet of paper as part of the design, as a result the fit was perfect.
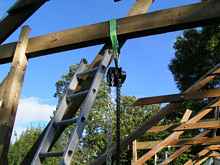 |
Views of the support beams and a chain hoist. The beams took a day to erect and 30 minutes to take down. |
I had measured the strops and decide that a one metre strop would hold the chain hoist in place and a six meter strop would wrap round the boat and connect to the hook on the end of the hoist, this worked out perfectly.
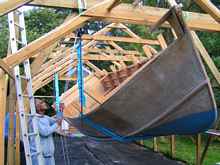 |
John doing most of the work while the rest of us supervise and catch the action on camera. |
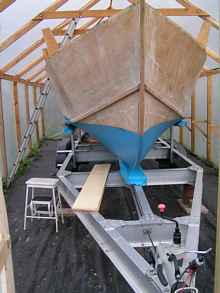 |
The boat in its final resting place (for now). Due to the cold weather I will not be doing much work over winter, a few jobs are possible like; fixing engine beds and bearers; cutting frames for the top side battens; cutting top side planking, etc… |
The turning method worked better than I had anticipated, the helpers were very useful – and hard working. Although I could have done the job myself by this method it would have taken longer and jobs like putting the cover on the boatshed with a bit of wind causing havoc would have been a nightmare. All my thanks go to the team, my wife Elizabeth, my brother-in-law John and his wife Gem, and friend David and his wife Raisa.
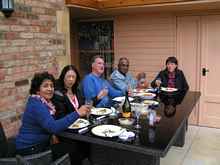 |
A perfect end to a perfect day. The team, except for myself taking the picture. |
If you want to see how this worked out, please watch the YouTube video below. Again thanks to members of the team for filming and John for editing.
*****
Click HERE for a list of articles by Mike Machnicki
|