Use of General-Purpose Adhesive Can Lead
to Premature Failure of Vacuum Infused Fiberglass Products
Resin flow or curing interference can lead to air pockets,
resin bubbles, and blisters. A vacuum infusion-specific adhesive
that crosslinks with the resin can offer greater interlaminal
shear strength.
The vacuum infusion process (VIP), a method using vacuum pressure
to force resin into a composite laminate, is widely used to create
lightweight, yet durable fiberglass components for everything
from yacht and boat hulls and to high performance racecar bodies.
In the process, adhesive is used to temporarily hold dry materials
laid into a mold until they're enclosed in a vacuum bag and resin
is injected. This is especially important on vertical or tight
radius work, where dry materials are prone to slip or move.
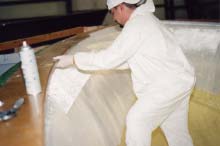 |
Design engineers use vacuum infusion for greater
quality, consistency, and performance than wet/hand lay-up
or vacuum bagging. It is ironic that general-purpose spray
adhesives can potentially negate these qualities. |
However, when general-purpose spray adhesive is used to hold
the layers of dry material together during the infusion process,
it may act as a contaminant that can ultimately compromise the
structural integrity of the part and lead to premature failure
in the field.
The general-purpose spray adhesives many companies use can interfere
with the resin curing process. They can even inhibit resin flow
if applied too thickly or unevenly, causing the resin to part
around that area like a rock in a stream of water. When this occurs,
air pockets, bubbles of resin, or osmotic blisters can form within
the structure of the fiberglass, making delamination or structural
failure more likely.
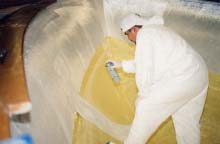 |
As a high strength, high temperature, solvent
based vacuum enabler for industrial use, Infuzene is designed
to safely fuse laminating materials to structural core surfaces,
forming a continuous matrix without structural weakness. |
Osmotic blistering, a form of composite failure that is a particular
problem in marine applications, occurs when water penetrates and
encounters a pocket of uncured resin. This results in a blister
of acidic fluid under pressure that will eventually break through
to the surface. Repair of the blisters requires grinding out the
blisters, thoroughly drying the hull, and patching the craters.
In many layered composites such as yacht hulls or turbine blades,
the structural risk can be particularly insidious if structural
weaknesses occur within internal layers, hidden from view. This
could lead to possible catastrophic failure without warning in
mission critical or high performance applications, such as yacht
or car racing, if no external signs of structural weakness are
presented.
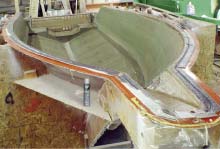 |
Since it will not interfere with the curing
process of vinyl esters, polyesters or styrene resins, Infuzene
allow resins to obtain maximum tensile sheer strength. The
adhesive crosslinks and hardens along with the ester or styrene
resins to form an integrated structure. |
For design engineers using vacuum infusion for greater quality,
consistency, and performance than wet/hand lay-up or vacuum bagging
offers, it is ironic that general-purpose spray adhesives can
potentially negate these qualities.
An adhesive product developed specifically for the vacuum infusion
process called Infuzene presents a solution by crosslinking with
the resin to provide greater interlaminal shear strength. Offered
by Port Orchard, WA-based Westech Aerosol, a specialty industrial
adhesives manufacturer, the vacuum infusion-specific adhesive
was developed to hold dry materials onto structural surfaces,
including vertical and tight radius work, during the vacuum infusion
process.
As a high strength, high temperature, solvent-based vacuum infusion
enabler for industrial use, it is designed to safely fuse laminating
materials to structural core surfaces, forming a continuous matrix
without structural weakness. Since it will not interfere with
the curing process of vinyl esters, polyester or styrene resins,
it allows resins to obtain maximum tensile shear strength. The
adhesive crosslinks and hardens along with the ester or styrene
resins to form an integrated structure.
In recent tests conducted by a leading independent university
composites testing lab, results indicated the vacuum infusion-enabling
adhesive provided a stronger bond in the vacuum infusion process
than the leading general-purpose spray adhesive. Based on ASTM
2344 short beam shear strength testing standards, the results
indicate that the composite with Infuzene was up to 30% stronger
in interlaminar shear strength than the same composite with the
leading alternative.
In the tests, seven plates were tested to failure under three
point bending. The MPa difference was +4.3 for light coverage
at 12.5 g/m2 and +7.0 for double coverage at 25 g/m2. The MPa
% difference was +18.53% for light coverage and +30.17% for double
coverage.
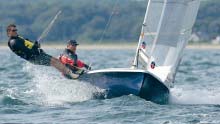 |
While the vacuum infusion-enabling adhesive
is primarily used for fibreglass, its crosslinking properties
with resin also provide greater interlaminar sheer strength
for carbon fibre (graphite) and Kevlar materials. |
In related tests, control specimens without adhesive failed at
an average of 50.2 MPa, while specimens with the vacuum infusion-enabling
adhesive failed at an average of 48.2 MPa at 12.5 g/m2, equal
to 96% of the control specimens. Though use of enablers in composites
typically results in some matrix strength loss, the vacuum infusion-enabling
adhesive resulted in significantly less matrix strength loss than
the general purpose adhesive.
In a separate osmotic test by CRITT Materiaux Poitou-Charentes,
a leading French testing firm, the vacuum infusion-enabling adhesive
was tested alongside an adhesive product already in use in the
yacht building industry. The result: "Product Ref. A (Westech
Infuzene) shows a superior resistance to osmotic ageing compared
to product Ref. B, which started blistering after only 5 days
of exposure to a laminar flow of water," concludes the report.
While the vacuum infusion-enabling adhesive is primarily used
for fiberglass, its crosslinking properties with resin also provide
greater interlaminar shear strength for carbon fiber (graphite)
and Kevlar materials. A canister system with a reusable gun and
hose eliminates the need for air-assisted application systems
and allows continuous application for large projects when a 13-ounce
can is insufficient.
For the most recent test results, including information from
the independent study, call 800-674-2010; Fax 360-674-2053; visit
www.ok2spray.com; or write to Westech
Aerosol Corporation at 5405 Constance Dr. SW, Port
Orchard, WA 98367.
Wesley Minor
Media Relations
Power PR
Phone (310) 787-1940 ext.117
Fax (310) 483-7313
E-mail:wminor@powerpr.com
*****

|