Today was a Saturday and so I got a lot done on the
'53 25 hp Evnirude.
click to enlarge
images |
After a 2 hour morning "paddle" aboard the Larsboat
on a local river, I comenced to working on the 25; first order
of business was to remove the carburetor for cleaning and rebuilding.
The carb on this 50-year-old engine is about as simple as these
things get; removing it required the disconnecting of the linkage
that synchronizes the carb butterfly valve and the magneto "spark
advance" and the removal of just two nuts. I always suggest
disconnecting linkages in such a manner so as not to disturb
adjustment settings, and so I merely removed a tiny cotter pin
on a bellcrank and unhooked a little tie rod.
After
removing the two nuts and also the fuel feed hose, the carb
was removed from the engine and dissasembled. All in all, it
did not look too dirty, but I went ahead and dropped it into
a gallon container of carb. cleaner to let it soak while I worked
on other things.
Usually
I just spray-out carbs with an aerisol carb cleaner, which is
the way that most engine manufacturers recommend cleaning late-model
carbs; in the old days, one allowed a carb to soak in cleaner
and then blew-it out with compressed air. A carb allowed to
soak for a day or two in the "old" carb cleaners came
out looking like brand-new, but it is difficult to find the
"old" cleaners now, as they have been replaced by
'environmentally-friendly" carb cleaners that do not clean
as well.
While
waiting for the carb to soak, I decided to replace the water
pump impeller. The six bolts that mount the lower unit were
removed, and the lower unit allowed to drop down to the extent
that the shift rod would allow. The shift rod is what connects
the shift lever on the Starboard side of the motor to the lower
unit, which is where the actual "transmission" is
located.
This
is where later OMC engines have an slight advantage; they usually
have a small access door in the side of the "tower"
or exhaust housing which allows one easy access to the coupler
that needs to be disconnected in order to remove the lower unit.
The Big Twin does not have such an access door. The coupler
is disconnected by allowing the lower unit to drop as far as
it can, and then by reaching into the open void between the
tower
and lower unit with a screwdriver and disconnecting the coupler.
Really no big deal when removing the lower unit, but a farely
major problem when re-installing it.
It is bad practice to carry a lower unit by holding the driveshaft;
in the case of this particular engine it, the driveshaft is
not secured into the lower unit by anything other than the tiny
key that drives the impeller.
With
the lower unit off the engine, the four screws securing the
pump housing were removed, and the pump housing and impeller
slid-up off the driveshaft. Most of these old OMC's have an
"O" ring sitting in a groove milled into the splines
at the
top
of the driveshaft. the purpose of this "O" ring is
to prevent water from rising up the driveshaft and getting into
the crankshaft bearings in the powerhead. The "O"
ring needs to be removed in order to remove and reinstall the
pump housing and impeller, but be sure to replace it once you
are finished with your waterpump work.
The
impeller removed from the engine was obviously "toast"
with the blades retaining a curled shape, and one blade retaining
a backwards-curled shape. Obviously, this impeller had seen
better days. With new impellers readily available from both
Johnson and Evinrude dealers, and also through aftermarket suppliers,
it just does
not make any sense to chance using an old impeller, even one
that looks in better shape than this one did. I installed a
new Sierra-brand impeller and reinstalled the pump housing and
also the "O" ring on top of the driveshaft. A SMALL
dab of waterproof grease was rubbed onto the driveshaft splines;
don't over-do it.
Getting the lower unit back onto the engine took a bit of "engineering."
One has to hold the lower unit just below the level of it's
installed position while one inserts the screw into the shift
rod coupler and tightens it, while also halding a flashlight
so as to see inside the engine. I hunted up a bolt of the same
diameter and thread as the lower unit's mounting bolts, but
which was longer, and used this long bolt to hold the lower
unit onto the engine but allowing about a 3/4 inch gap between
the mating surfaces which then allowed me to focus a flashlight
on the couple while I inserted the screw using a magnetic screwdriver.
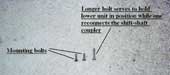
Once the coupler was fastened, I secured the lower unit into
place with it's proper mounting bolts and removed the one long
bolt. Although dealing with the coupler is easier on MOST later
OMC's, one advantage of this older engine is that it did not
utilize a water tube for conducting water from the pump up into
the powerhead, and dealing with the water tube can sometimes
be difficult on the later engnes. Onc must simply take one's
time and not allow frustration to take-over when reinstalling
lower units.
At
this point I went back to the carb, which had been soaking for
about an hour or so. The passages in the carb were blown-out
with aerisol carb cleaner (BE SURE TO WEAR EYE PROTECTION !!!)
and I went looking for a carb kit. The Sierra catalog does not
list a carb kit for a '53 Big Twin, but does list a kit for
'54s. I used a "54 kit which had many extra parts not needed
for the '53, and I needed to trim the bowl gasket a bit with
a razor blade in order to make it fit, but I did replace the
parts that needed replacing;
primarily
the bowl needle and seat, the afore-mentioned bowl gasket, and
the packing that seals the high - and low speed needle valves.
The existing float looked OK, as most do; keep in mind that
these old cork carb floats are coated with varnish, and that
carb cleaner is intended to remove varnish, so keep the cleaner
away from the float..
The
reassembled carb was bolted back onto the engine and the linkage
reconnected. On these old OMC engines, the twist-grip throttle
is connected to the magneto, and advancing the twist grip advances
the magneto timing. The linkage connecting the carb butterfly
(throttle) valve needs to be synchronized to the magneto in
order to obtain the best performance. On this engine, as on
so many old OMc's, that is a simple matter of lining-up a mark
on a sheet-metal "cam" screwed to the underside of
the magneto, with the roller or follower on the linkage for
the butterfly valve. One retaining hole in the sheet metal cam
is slotted so that the cam may be moved in and out, and the
cam is moved so that, when the butterfly roller is next to the
mark, any slack or "looseness" in the linkage to the
butterfly has been "taken up" and the butterfly shaft
itself just begins to move. Making this adjustment takes all
of 5 minutes and requires no tools other than a small wrench
to fit the cam's retaining screws.
Now it was time to finally reinstall the
magneto, a procedure made considerably more complicated by this
early engine's tension-cable linkage to the twist grip. As previously
mentioned, later engines use a shaft and bellcrank arrangement
which is much easier to deal with. Other than getting the cable
back onto it's sheaves, mounting the magneto involved no more
than placing it down onto the crankshaft, being mindful of not
allowing the "followers" on the new ignition points
to "hang-up" on the cam which actuates them, and refastening
the four screws which secure the magneto. The flywheel was set
in place and lightly secured by it's nut, then the flywheel
was slowly rotated by hand to insure that the coil "heels"
did not make contact with the flywheel magnets (they did, and
the flywheel was removed and the coils moved back away from
the flywheel a merest thousand of an inch; see magnetos
column for more details)
With
the flywheel again set on the crankshaft and the nut hand-tight,
"flipping:" the flywheel by hand produced sparks from
both sparkplugs. A magneto that sparks this readily makes engine
starting less of a chore.
With about 3 1/2 hours expended on the engine today, the replacement
of old fuel lines will wait until the next session, amd at that
point the engine will be about ready for the initial starting
attempts. Once the engine has (or has not) proven that it will
run, I will then have a look at the recoil starter to see what,
if anything, it needs.
Max
Continue
on to Part 3....