"How to Build a Better Butt"
Lately, there has been some lively discussion
concerning the building of ‘larger’ boats. That
is, those that require planking, bottoms, etc., of a length
greater than the ‘standard’ 8 feet of sheet goods.
This may be due to the onset of cooler weather and everybody
getting prepared for the winter ‘building season’
as opposed to the summer ‘sailing season’.
As an adjunct to this, there has been conversations extolling
the virtues & economy of ‘butting’ large pieces
together, rather than the ‘modern tradition’ of
scarfing.
My own preference is for the scarf joint. I know the theory
of making a butt joint - from the simplest ‘plank backed’
to the more elegant & recent epoxy/glass Payson joint -
and don’t disagree with it’s functionality.
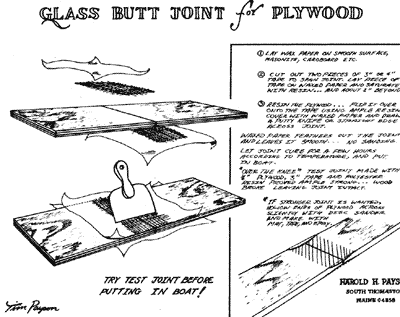
Payson Joint (click to enlarge)
I guess my reluctance comes from where I first saw an example.
I was visiting an individual {a frequent & valuable contributor
to the on-line Groups, and may very well be a ‘duckworks’
subscriber}, who was showing me his latest ‘pride &
joy’ before delivery to a customer. An original design,
and really nice work. The dark finish of the hull was a smooth
high gloss. As I walked around, from the Port side toward the
Bow, the hull glistening in the afternoon sun, the outline of
the interior butt block simply jumped out. It was if it was
a raised area on the hull. I continued to walk around the boat.
Then I took out and unfolded my handkerchief, put it over my
palm, and gently rubbed across the area of the block. {an old
trick to see if bodywork has been done on a car}. I don’t
remember if I could feel anything . . . but you could DEFINITELY
see it in a glancing light. This would have been invisible &
inconsequential on a thick ply bottom, where the beam-to-beam
butt strap would have functionally acted as a foot rest but
on a side panel it made the entire job seem amateurish.
Be that as it may, and I do agree that there are places that
are excellent applications, the following ‘conversation’
recently occurred . . .

From: "timk_smith"
To: <quohog@att.net>
Subject: butt joints
Date: Friday, September 10, 2004 16:37
Dear Ron,
You very kindly sent me a thorough explanation some time ago
about how you make butt joints in plywood panels, glassing both
the top and the bottom at once. I wonder if I could trouble
you for some follow-up advice.
I made a test panel the other night using your method with
pieces of half-inch ply and three layers of tape, the ends of
the panels pared down a little with a router to take the tape.
The joint is immensely strong, but there are some air pockets
in it, small, about one inch by half an inch, and there are
spots where the tape moved a bit and pulled away from the sides
of its channel. I suppose I didn't get a perfect squish and
should cut a hair less deeply with the router. But I also suppose
that joints made this way always have a few imperfections. My
question is, is it structurally sound to sand out any air pockets
and those voids and any others using either bits of tape or
thickened epoxy? More generally, do joints of this kind usually
need a bit of such fiddling? (The panels will get layers of
cloth on both sides once they are joined up.)
Best regards,
Tim Smith
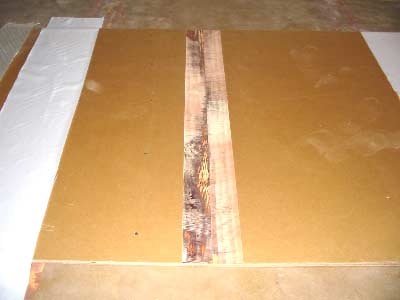
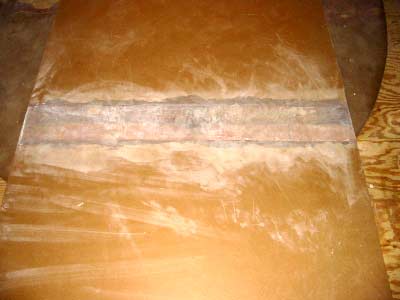
Note: This is Tim's joint -
I did not see these pictures until later
From: "Ron Magen" <quohog@att.net>
To: "timk_smith"
Subject: Re: butt joints
Date: Sunday, September 12, 2004 14:27
Tim,
Glad I was able to help you. The actual credit for the concept
of the joint comes from the ideas of a lot of people. It was
illustrated and 'popularized' by Dynamite Payson. I got it in
an addition to the
original plans for Bolger's 'Rubens Nymph'.
The caveat to this is that, to my knowledge, the method is
for the joining of the thinner, more flexible, 1/4 inch ply.
Although I'm sure it has been done, it is not what I would use
for the much stiffer ½
inch material. ESPECIALLY if you have 'rebated' the ends of
the material at the joint. While it may seem effective in a
flat, or straight orientation, the square edges of the 'channel'
are stress points of
incipient failure.
The joint is supposed to be made with a shallow 'swale' produced
by a disk sander. {As in the simple type that are clamped in
an electric drill} This is so there is a smooth transition from
the surface plane of one sheet, dipping down at the actual juncture,
then back up to the surface plane of the second sheet. There
should be NO 'square' or sharp edges.
For the thicker ½ inch material I would use a scarf
joint. More so, if you are willing to go to the time & trouble
to rout a flat on each sheet. A decent scarf joint {8:1 or 12:1}is
much easier to produce. Simply 'stair-step' the two sheets,
then hand plane or power-sand them to a uniform angle. Gluing
them is simply a matter of clamping one sheet down, painting
on some unthickened epoxy, mixing some filler into the remaining,
'buttering' that on, lining up the second sheet with the first,
and clamping that one.
As far as your specific problem . . . the 'channel' gave room
for the glass & epoxy to move. When in it's fluid state,
the epoxy acts like a lubricant. When the 'epoxy butt' joint
is used with thicker materials, the first layer is a piece of
EPOXY matting or woven roving. This is worked into place with
a 'bubble roller' to drive out air & fully saturate the
stuff. Then a piece of cloth is rolled into place, followed
by a wider piece that overlaps the whole. This way the bubbles
and wrinkles are worked out, and 'escape' via the sloping sides.
The joints shouldn't need any 'fiddling', they are so simple
{by using the router, you did more work than is necessary}.
A 'bubble' roller is handy, but a simple plastic squeegee will
do the job. Depending on the size of the bubbles, the quantity,
their location, and your sensibilities, you can dig them out/open.
Fill them with a mixture of epoxy, fumed silica, and milled
fibers. 'Mayonnaise' of a thick cream consistency will give
'self leveling'.
I'm trying to diagnose the problem without actually seeing
the 'patient'. Any number of the boat suppliers have catalogs
with much, if not all, of this stuff listed & illustrated.
If you need more detail,
I'll try to dig out the page with Payson's sketch and scan it.
Regards & Good Luck,
Ron Magen
Backyard Boatshop
- - - -
From: <timk_smith@
Ron,
Thanks for this. All very sensible. The panels are for a Bolger
Topaz, and in the building guide Phil and Suzanne actually specify
a Payson-type butt joint for half-inch ply. Did one last night
with a slightly shallower rout, will see how it turned out when
I go home.
Thanks again,
Tim.
- - - - -
From: "Ron Magen" <quohog@att.net>
Tim,
WHERE is that butt joint going? If it is for a FLAT 'surface'
like a bottom, then I would have no concern. However, if it
will be in a CURVED panel it will give a 'flat spot' in the
fairness of the shape. Also a stress point. The greater the
curve . . . the more of a 'hitch' and greater the stress. It
will become more obvious if a fine, high gloss finish is applied.
Bolger's 'attitude' has always been toward MAXIMUM efficiency.
"Use everything but the squeal", so to speak. Therefore
he gives layouts for 4x8 sheet goods that use as much of the
material as possible. This often means butt splicing the forward
4 feet of a bottom to the aft 8 feet - where the aft part is
almost as wide as the sheet, and the fore part is the corner
of another where many other smaller parts are laid out.
This is opposed to the 'loss' of a couple of inches of sheet
goods in the scarfing process. About 95 percent of the people
on this forum will agree that to skimp on materials is often
foolhardy. All of them combined are usually only a fraction
of the cost & value of the time & energy put into the
total. If I was working with $200 a sheet ply . . . I might
think about it. Then on the other hand, if I was putting that
kind of material into a project, I would want to do the ABSOLUTE
BEST work I was capable of. Only ONE joint? If you are using
½ inch ACX . . . we're speaking about what - $25 for
the less then half a sheet 'remainder'? There are a LOT of 'odds
& ends' that can be made from that. A bit of stain, epoxy,
& varnish and 6inch square pieces become nice looking backing
blocks for deck hardware, a larger piece becomes a motor mount
board, etc.
Don't worry about the router, get a $5.00 'disk sanding attachment'
for your drill and make another test piece. {Of course if you
have an 'angle grinder' or a Random Orbit Sander . . . use that
with some 60 grit}.
Regards & Good Luck,
Ron Magen
Backyard Boatshop
- - - - -
From: <timk_smith@
Ron,
The good news is that I unpacked the dried joint last night-made
with a slightly shallower rout-and it came out very nicely.
No air bubbles to speak of, three layers of tape nestled neatly
in glue on both sides.
These are the boat's side panels, and they will be curved-four
sheets joined end-to-end. I am a little concerned about flat
spots, though when I picked up one end of the two-sheet assembly
last night it seemed to curve fairly. Is the width of the tape
in a joint like this a factor? For this design Bolger says to
make taped butt joints using a power plane of three inches;
that seemed so narrow to me that I went with six inches instead.
I made a couple of the butt joints for the roof panel using
an angle grinder. Because the grinder gives the irregularities
of freehand work, I switched over to the router and got more
predictable results. That's why I wanted to use it applying
your description of the Payson joint-since the underside is
assembled "blind," I thought it would be a good idea
to build predictability into the process. (The router is no
more trouble to use; I have a good edge guide and it takes only
a few passes).
But if you think flat spots will be a problem, maybe I should
switch back to the grinder and use narrower tape.
--Tim.
- - - -
From: "Ron Magen" <quohog@att.net>
Tim,
I'm really at a loss here. There are no pictures, so I can only
go by your verbal descriptions as to what you are doing.
It is only a guess, but the probable reason for no bubbles
in the shallower 'channel' was that you were able to apply more
pressure on the epoxy saturated material. This squeezed out
the air.
Regarding the 'flat spots'. They become more noticeable with
the severity of the curve, and the smoothness & gloss of
the final finished applied. The width of the tape is a factor
- the narrower the tape the more abrupt the transition between
the sheets. In addition, from a structural standpoint the greater
the stress on the actual joint. The wider the tape and application
the more contact area for the 'glue' and the more the stresses
are spread out. This is one of the reasons a scarf joint is
done on an 8 to 1, or 12 to 1, slope - rather then an abrupt
45 degree cut.
I'd really like to see exactly what Phil is saying, and in
what context, when he refers to a, ". . . using a 3 inch
power plane . . .". The reason is that a lot of people
recommend the use of a power plane to CUT SCARF JOINTS. {Plus,
12 x 0.25 = 3 . . . the length of a long scarf in 1/4 inch material.}
I don't own a power plane. If I had to make a large number of
joints, my tool of choice is an in-line belt sander. This is
much more of a multi-tasking device, as opposed to the purpose
built plane. That being said, I do my scarfing with a Surform
tool and a sharp Jack plane.
I mentioned the angle grinder because it is another handy tool.
Like the belt sander & power plane, it takes a bit of practice
& a LIGHT touch to do finesse work. Also the CORRECT 'head'.
There is a specific type of 'disk' called a 'flap disk' {NOT
the square edged 'flap sanders}. Some of the people who make
Windsor chairs use them to make the 'hollows' in the seats.
The same technique would be used here. The disk held at an angle
to the surface & 'rocked' back & forth in a gently curving
motion.
A Random-Orbit sander could also be used, or the simplest disk
sander attachment for an electric drill. Where did the plans
come from? The reason I ask is that I dug up my drawing from
Dynamite Payson illustrating the method - it came with either
a 'Study Plans' packet, or with a set of plans.
You shouldn't use narrower tape, actually the opposite. "If
stronger joint is wanted, hollow ends of plywood across slightly
with disk sander and make with mat, tape, and epoxy." These
are the EXACT words on the drawing. Because the instruction
above this talks about an "over the knee" test with
1/4 ply, 3 INCH tape, and polyester resin . . . while the hollow
technique specifies epoxy . . . I believe the drawing is *relatively*
recent. If I was working with ½ inch sheet goods - and
couldn't use a scarf - I'd be using 4 to 6 inch wide pieces
of glass fabric for my top layer.
Remember, there is NO PROBLEM with ' freehand irregularities'
when working with epoxy. In fact, joints that are 'too tight'
can cause epoxy starvation. The top surface is what you will
be manipulating, and that should become smooth. 'Predictability'
comes from the testing you are doing, plus thinking about how
you are going to handle the full scale pieces, then arranging
everything at hand before you actually begin. Maybe even a few
'dry runs'.
Regards & Good Luck,
Ron Magen
Backyard Boatshop
{I'm going to try and scan or photograph the sketch and attach
it}
[insert ‘Payson Joint’ drawing here]
- - - -
From: <timk_smith@
Ron,
I don't mean to keep lobbing puzzles at you, sorry. I've made
Payson-type joints before, successfully, albeit in thinner ply--it's
just that I usually make them one side at a time, so I can see
what I'm doing. I have the right flap wheel for the grinder
and made the Payson joints for the roof panel with it. Came
out fine.
The joints in the half-inch ply seem to be coming out fine,
too. I've bent the panel pretty severely and find no flat spots.
I felt the same way you do about the width of the tape, so widened
it out to six inches in three layers--inside layer of 12-oz
tape, followed by two layers of 6-oz. So far so good.
The study guide is from Bolger, though I'm pretty sure Suzanne
wrote it--Topaz, I'm told, is really the first design from PB&F
that's "hers." if you're really interested I'll copy
out the portion I'm describing and e-mail it to you.
Thanks for all your help with this.
Best,
Tim.
- - - - -
From: "Ron Magen" <quohog@att.net>
Tim,
It's your boat, and you are the one who has to have confidence
in it's construction. It's no 'puzzle' - you have well described
what you are doing - it's just that the methodology seems awkward
to me. It almost could be called a 'double lap' joint. The concept
of a single pass with a 3 inch power plane {with the sheet junction
centered}, seems to be a condescension to a 'quickie' way of
doing it. I don't know of 'Topaz', but anything that has ½
inch thick side panels and cabin with a 'roof', certainly isn't
an 'Instant Boat'.
Once again . . . *MY* personal preference would be to use a
scarf joint. Probably no more effort and maybe only a touch
more time. {Using the 'stair-step' technique, they would be
all cut at once} It might 'cost' a couple of more sheets of
ply - due to the few inches of 'shortening' in the overall sheet
length - but it would be minimal compared to the total cost
of the completed boat.
If this is what 'they' *SPECIFY* {and illustrate with sketches},
and you would rather not question them about it, then it's your
choice. No matter 'who' drew/designed it, "Phil & Co.'
stands behind the work.
Regards & Good Luck,
Ron Magen
Backyard Boatshop
{PS - could you send me the EXACT wording - and context - plus
any sketches of the joint}
- - - - -
From: <timk_smith@
Ron,
Topaz is a "poor man's picnic boat," 31 feet long
with an octagonal house and a forward cockpit (there's a lines
drawing in one of the Bolger group folders).
The exact wording for the sides is "assemble with Payson-type
butts (if they're scarfed they won't come out of four panels)."
That is the second reference in the building guide to joining
half-inch panels with Payson butts. The first is in the guide
to building the bottom, which is made of two courses of half-inch
ply and takes a strong curve forward. The wording for that,
referring to a single course, is: "...Lay out flat...with
Payson-type taped butts as diagramed. [they enclose the same
diagram you sent me]. Use a power-plane of 3" to hollow
out the plywood to take two layers of tape bedded in epoxy flush,
with no protrusion especially on the side that will take the
second course."
I've made mine a little differently, six inches wide, with
an extra layer of biaxial tape under two layers of lighter woven
stuff. If it would help for the column, I could send a couple
of pictures.
Best and thanks again,
Tim.
- - - - -
From: "Ron Magen" <quohog@att.net>
Tim,
'Topaz' is certainly an ambitious project !!
However, the wording of 'their' instructions proves my original
supposition. The individual who wrote them is either NOT a 'tool
user', or had fallen into the 'More Power !!' trap in trying
to help you . . . with an incomplete explanation.
The reason for choosing the 'Butt' over the 'Scarf' is as I
first suggested - it fits with their {?} philosophy of efficiency
- ' . . .if they're scarfed they won't come out of four panels'.
The suggestion that you use the 'Payson Joint' {and including
his son's sketch} was to illustrate the proper technique. Where
it became confusing was in the 'instruction' to use a 3 inch
power plane. To sand a 'swale' across a sheet of ½ inch
sheet goods takes a bit of time & effort. Plus, the specific
note on Payson's diagram {about a drill-mounted disk} may be
cheap, and effective for 1/4 inch material, but is not the most
efficient for ½ inch. In addition, what *may* have been
clear in their mind, WASN'T complete on the page. This led to
confusion for the reader {YOU} who wasn't intimately involved
with the varied use of many tools.
While I would approach it a different way, here's what I THINK
was meant {and it's what I would do if I HAD to use a 3 inch
power plane}.
1 - Use the power plane to make a 3 inch wide cut on the end
of EACH SHEET !! Make the cuts on an angle, so that when they
are butted together there will be a 6 inch wide, shallow 'V'.
{1a - at this point I would butt the pieces together and use
a flap disk & angle grinder to 'soften' the angular 'V'
into a swale}
2 - Butt the pieces together and 'paint' the cut area with
unthickened epoxy
3 - Lay a 3 inch wide strip of cloth - centered over the joint
- across the panel. Roll down with a 'bubble roller' and add
more epoxy as necessary to saturate.
4 - Repeat, with strips 4 and 6 inches wide - the final piece
covering the entire cut area. Roll down & add epoxy as necessary.
{you used 3 pieces - I would have used light mat, then 4, and
6 inches wide strips, respectively}
5 - Lay a wide piece of heavy plastic over the lot and roll
down with a length of heavy PVC pipe {use like a big rolling
pin}
6 - Place a plank wide enough to cover all {or a piece of ply
with a heavy plank on top} and clamp in place.
As I stated at the beginning of this note - it's an ambitious
project. She WILL NOT be 'built in a day'. Plan ahead how you
will fabricate each segment . . . and don't scrimp or cut corners
with time. Rather then concern yourself with doing both sides
perfectly AND simultaneously - do ONE side at a time. OR, consider
one side 'primary' {the exterior side that will be seen by the
'public'} and don't concern yourself with whatever cosmetic
imperfections occur.
From your last paragraph, I get the impression that our discussion
is moot. You seem to have already done the job. If so, why question
the technique now? I don't think you are about to do the work
over - no matter what I say.
Thanks for the offer of the photo's
Regards,
Ron Magen
Backyard Boatshop
- - - -
From: "Ron Magen" <quohog@att.net>
Date: Wednesday, September 29, 2004 10:18
Tim,
Haven't heard from you for a while.
As I said, an ambitious project . . . how far have you progressed
?
Regards,
Ron Magen
Backyard Boatshop
{PS - how has the remnants of Jeanne affected you ? We got about
10 inches of rain yesterday night. Basement stayed dry - so
all I did to the house & surroundings worked . . . Interestingly,
Joanne mentioned that having two boats in the yard was ‘nice’}
- - - - -
From: <timk_smith@
Ron. I'm grateful as can be for your advice.
I'm plugging away, but haven't gone 3-D yet. Have fabricated
the bulkheads, house top, house sides, and most of one side
panel (that's the one I queried you about). Still getting good
results with my wacky method, which turns out to have an advantage:
the hard corners of the routed declivity keep the glue in the
joint when the whole works is compressed. Another thing I forgot
to mention is the importance of doing both sides of the joint
at once when working alone. When there are multiple butt joints
in a panel on just one side, flipping the panel without cracking
the joint can be quite a project.
At any rate, I enjoy our correspondence (and your columns).
If it would be any use to you, I could send you some photos
of the joints.
best,
tim

And there it stands . . . so far. As Tim indicates, while a
number of parts have been fabricated they are still in ‘2-D’.
That is, as cut out & shaped flat surfaces. While they obviously
have their epoxy & glass butt joints, I don’t know
if they are also glass sheathed. While Tim may decide to sheath
them ‘in the flat’ {a rather neat & efficient
way to get a good, level job}, the final finish will be applied
when the boat is in the last stages of construction. THAT will
be the absolute proof.
Ron Magen
Backyard Boatshop
[PS - I recently used long, horizontal butt block joints to
fabricate the sides of a raised flower bed, for Joanne. Rather
then buy ‘new’ planking, I was ‘instructed’
to use some old, odd-sized, trim edged planks that have been
laying in the shop overhead for YEARS. She got inspired when
‘we’ decided to clean out that area. She was fascinated
by the method and liked my Stainless screws so much . . . told
me to ORDER MORE !! . . . a) I guess she has plans, and b) you
never know where you’ll be using those boatbuilding skills
& techniques]