Applying Epoxy Coatings Underwater
and On Wet Or Damp Surfaces
By Paul Oman
Underwater painting sounds like
some sort of parlor trick, but there are actually a number of
epoxy coatings ad repair products that can be applied to damp,
wet, saturated, or submerged surfaces as well as used in environments
of very high humidity. Typical work sites can include pits, sumps,
underwater supports, boats, piers and pilings and all sorts of
below grade structures. The ability to patch, seal, encapsulate,
reinforce, and protect objects, in place and in wet environments,
is a much more attractive option than the alternative which is
usually demolish and rebuild from scratch.
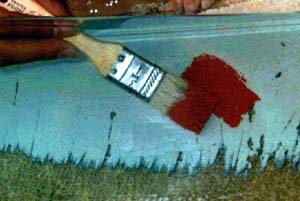
Despite the obvious advantages
of moisture tolerant coating/repair products, such epoxies are
not widely known or understood. The concept of underwater painting
remains out of the belief of most industrial and marine maintenance
professionals. However, with a slowing economy and fewer replacement
dollars available, in situ rehabilitation or repair of existing
structures, be they docks, yachts, ships, or dams, is becoming
more of a more likely option. In some cases the object might not
be exactly underwater, just water saturated. An example would
be an empty cement pit, manhole or sump that has contained water
for many years. The cement is completely water saturated and will
remain so for a very long time.
Epoxy Basics
First formulated in the late 1930s
in the U.S. and Switzerland, epoxies can be considered a two-part,
thermoset plastic. Mix two liquid components together, a heat
producing reaction (known as ‘Exotherm’) occurs, and
a hard product results. Some basic and general characteristics
of epoxies are: 1) easy cure temperatures, generally from 5-150
degrees C; 2) low shrinkage; 3) high adhesive strengths; 4) high
mechanical properties; 5) high electrical insulation; and 6) good
chemical resistance.
With so much going for it, epoxies
were produced as commercial adhesives in 1946 and as commercial
coatings by 1947. The versatility of epoxies was further advanced
with the early formulations of epoxies that could be applied in
an uncured state to wet surfaces. These special epoxies have evolved
from rather crude, unfriendly products into high performance,
applicator friendly coatings.
Epoxy Curing Agents
The curing agent selection plays
the major role in determining many of the properties of the final
cured epoxy. These properties include pot life, dry time, penetration
and wetting ability. Curing agents come in many different chemical
flavors, generally based upon amines or amides. Amine based curing
agents are considered to more durable and chemical resistant than
amide based curing agents but most have a tendency to ‘blush’
in moist conditions. Blushing produces a waxy surface film on
actively curing epoxy, the result a reaction with the curing agent
and moisture in the air. Other potentially toxic chemicals within
the curing agent can also be released in the same manner, thus
amines are often viewed in light of these potential shortcomings.
Amides, on the other hand, are more surface tolerant and less
troubled by moisture. Fortunately for epoxy end-users involved
with underwater applications, there is a small subgroup of non-benzene
ring structured amines that maintain all the benefits of amines
while removing the toxic leachability and moisture attracting
properties of typical amines. These special polyamines form the
basis for today’s cutting edge underwater epoxies.
How Epoxies Work
The well known adhesion of epoxies
is due to the strong polar bonds it forms with the surfaces it
comes in contact with. On dry surfaces the bond between the surface
and the epoxy displaces the air, which is a fluid. The same is
true underwater. As on dry surfaces, the polar bond attraction
is strong enough to displace the fluid, in this case the water,
and produce an strong bond even underwater. Thus, painting underwater
is, in theory, no different that painting above the water. The
cross linking reaction of epoxies should be independent of the
surrounding environment. Still most curing agents will react with
water molecules rather than the epoxy base, resulting in a waxy
film, mentioned above, known as amine blush. This makes them unsuitable
for underwater application.
A WARNING: Always Test First
(Cathodic Issues)
Epoxies bond to surfaces at the
molecular level by tiny electrical charges. Sometimes in marine
settings there can be pre-existing electrical charges in the underwater
environment that interfere with the bonding mechanism of the coatings.
Such electrical cells can be either intentional or accidental.
Active or passive cathodic protection
systems, designed to protect against underwater corrosion, will
produce electrical fields that disrupt coating bonding. Dissimilar
metals in the immediate vicinity (identified or unidentified)
will also produce stray electrical fields. Even chemicals and
pollution in the water may be responsible for or enhance the voltage
of existing underwater electrical cells. The problem is more often
observed in dirty harbors, full of unidentified metal junk, and
chemical/industrial waste. Even ongoing arc welding on a ship
will produce electrical charges on and around the hull. Ships
tied to dockside facilities with their own cathodic protection
systems or sloppy electrical systems, can cause underwater coating
bonding problems on conductive (metallic) surfaces. Generally
there is no problem on non-conductive surfaces such as concrete
and wood, or in fresh water.
The method to evaluate the application
and bond of underwater coatings on conductive metallic surfaces
in seawater is not in a bucket of harbor water, but under actual
conditions. What bonds and works well at Dock A, may not work
at Dock B or when tied up to Facility C due to identified or unidentified
electrical charges at that site.
Almost without exception, bonding
problems associated with ‘underwater painting' are site
specific and related to electrical cells formed in a conductive
medium (seawater) on a conductive surface. Always test in the
actual marine environment before committing to any underwater
coating project.
If there is a problem, the epoxy
will simple refuse to ‘stick’ to the surface. It is
very obvious (and embarrassing). It often will not transfer off
the brush, roller, or paint pad/glove..
A WARNING: Always Test First (Additives
in Concrete)
Concrete structures, often commercial
in nature, can sometimes have adhesion problems too. Commercial
aquariums and swimming pools are examples. In some cases chemicals
were added to the concrete to speed curing, reduce air bubbles,
etc. These chemicals, some perhaps silicon based, prevent bonding
of the epoxies to the concrete. It is also possible (I don’t
have proof) that some pool/aquarium paints also contain stain
or slime ‘no-stick’ chemicals that make underwater
coating impossible. I know of commercial aquariums where some
the underwater epoxies work fine and others where they don’t
work at all. The only safe thing to do is test before taking on
such a project.
Epoxy Evolution
Three generations of apply underwater
epoxies have emerged over the years. Each has pushed the technology
window forward. The success of first generation epoxies was in
their ability to be applied and cured underwater. The next generation
moved these epoxies into true coating status, albeit with issues
of user friendliness and chemical safety issues still to be addressed.
The new third generation epoxies have addressed those issues successfully.
First Generation Underwater Epoxy Coatings
-
Sticky, like Bubble Gum
-
Knead the two parts together in hand-sized
amounts and push on to the surface
-
Potentially difficult to ship - may require
haz-mat shipping (Corrosive Liquid -N.O.S.)
-
May have short shelf life.
Second Generation Underwater Epoxy Coatings
-
Good underwater adhesion
-
True bonding instead of sticking
-
Poor storage stability (heating required)
- products tended to crystallize over time
-
Toxic - MDA and possible solvents
-
Haz-mat shipping required
-
Problem bonding to cathodically protected
surfaces
Third Generation Underwater Epoxy Coatings
-
Stable storage - will not crystallize over
time
-
Basically Non-toxic, 100% solids (0% VOC),
no MDA
-
Non haz-mat - unregulated shipping
-
Improved application on cathodically protected
surfaces
-
Easy application results in productivity increase
Underwater Epoxies in Action
-
A Recent (12/02) example in the user’s own words
Subject:
Underwater Epoxy Repairs - Follow-up Report
From: Joy Sxxxx <bansheeboat@xxxxxxx.xxx>
To: p.oman@ix.netcom.com - Progressive Epoxy
Polymers, Inc. www.epoxyproducts.com
Paul:
Remember me?
Joy Smith and her sunk boat in Papua New Guinea around Christmas
time last year?
By the time I finally left
my boat and got off the island, got to civilization and then
found your website, in my desperate search for an air-shippable
underwater epoxy, we had been marooned on remote Hermit Is.,
PNG for two months. Banshee sank on October 21, 2002, in three
minutes, after hitting a coral head and was completely underwater
for three days. There was a 6 ft. crack through the hull and
a punched in hole about a foot in diameter. The damage was massive.
Leslie patched the hull with
old Z-Spar Splash Zone and a piece of wood a villager shaped
with an axe. We kedged it off the reef, winched it upright,
and then the villagers built an underwater cradle of lashed
together logs to support Banshee. We bailed with buckets during
a very low tide at night. She floated. The inside of the boat
was trashed, the electric/electronics destroyed, the engine
unusable, lots of things stolen, and diesel oil, sandy sea water
and ocean bottom rubble and mold covered everything. But the
sailing rig survived.
However, it soon became apparent
that the old Z-Spar patch would never hold for a 300 mile open
sea voyage to Madang, PNG and dry dock for hull repair. As I
told you when I wrote in December, the hull was steadily leaking,
and we knew the temporary repair would not last much longer.
I was desperate to save my
boat that has been my life for 32 years.
I bought your underwater
epoxy, and you shipped it to Manus Is., PNG. I picked it up
and returned to the remote island of Hermit-what a name!! Almost
didn't make it back as a storm came up while we were in the
open 26 ft. boat making it back to the island. 36 hrs in an
open boat with heavy seas with local bush people and me! BUT
I HAD THE EPOXY AND KNEW WE WOULD NOW SAIL BANSHEE OFF HERMIT.
The whole saga is a very
very long story of an incredible three month ordeal for two
women alone. I got back to Hermit in mid January, and Les and
I applied your stuff according to your directions. We patched
the hull inside and out as you said. By then, the leakage from
the 10 year old Z-Spar Splash Zone was getting worse. However,
your stuff stopped all the leaks.
After 3 weeks of working
on the boat, we left Hermit for the voyage to Madang, PNG. Sailing
the 300 miles with no engine, no electronics, no autopilot,
no functioning life-raft, and very little food or water. There
were very high winds and rough seas and then dead calms, and
we only had wind and sails alone to get us across that ocean.
YOUR REPAIR STUFF HELD!! The hull had a fierce pounding-but
no leaks. WE MADE IT!! We were towed in at the entrance to Madang
Harbor and collapsed in exhaustion.
If we had not had your epoxy
- our boat which is our life would still be under water at Hermit.
We owe a debt of gratitude to you. The boat was put up in a
primitive dry dock, and we literally cut out the repaired hull
with a diamond tipped saw. Your stuff eats sanding grinders!
We are good at epoxy repair of hulls-thank goodness, because
no one here knew anything. Before we had properly repaired big
holes where thru-hulls had been removed by building up larger
and larger layers of mat and roving with epoxy resin. Leslie
is very good at that-having worked in a fiberglass repair shop.
This was just a bigger job.
Ghastly work. We have pictures
of the repair and the 6 ft. long crack and hole in the hull.
We are now safely sitting
in an anchorage in Madang rebuilding, and rewiring with our
very limited funds. We plan to leave Madang for Guam and employment
in December....
Very thankfully,
Joy S. and Leslie B.,
US Yacht Banshee
Madang, Papua New Guinea
Manufacturer Notes
There aren't a lot of formulators/manufacturers
making underwater epoxies. It is a small niche with generally
limited sales. Often underwater repair jobs require as little
as 1 quart of epoxy, or perhaps 30 or 40 gallons - not enough
volume for many of the larger companies. Besides the small volumes,
the cathodic bonding problems mentioned above require distributors
to do a lot of handholding and pre-sale testing - simply a lot
of extra work and effort put into problem avoidance. Also the
epoxy raw materials are generally more expensive than other epoxy
raw materials meaning a higher priced product or lower profit
margins. It is easy to see why large coating companies would rather
focus on high volume epoxies and leave the niche underwater market
to the smaller specialty companies.
Closing
The underwater applied coating
market remains a small niche within the much larger industrial
and marine maintenance marketplace. Both first and second generation
underwater coatings are still widely in use, primarily because
of the conservative nature of the industry and the acceptance
of less than user friendly underwater products. Too few users
and potential users/applicators of underwater coatings are aware
of the advances made in recent years. This is changing as the
shift toward environmentally friendlier, and easier to use coatings
are slowly causing the re-evaluation of old familiar products
and the introduction of new companies with new products that better
meet today’s expectations. The ability of a single product
to be effectively used on dry surfaces, underwater, or on saturated
or dripping metal/concrete surfaces, while being both environmentally
and user friendly, represents a technology that will continue
to gain acceptance. The savings associated with in-situ underwater
repairs and coating projects is often easy to document, as are
the potential benefits from even more ambitious applications of
this maturing coating technology.
* Paul Oman - Progressive Epoxy Polymers, Inc.
48 Wildwood Dr. Pittsfield, NH 03263 603-435-7199 Fax/435-7182
info@epoxyproducts.com
- www.epoxyproducts.com
Who Are We? Learn more about us at: epoxyproducts.com/pep.html
----------
APPENDIX: Underwater epoxies (also regularly
used on dry surfaces) offered by Progressive Epoxy Polymers, Inc.
(in unit sizes as small as one quart) include:
1) Quick Fix 2300
- non hazmat quick setting epoxy paste (will work in cold water);
2) Wet Dry 700
- non hazmat epoxy paste with normal potlife and cure times; Our
Wet Dry 700 epoxy paste is representative of the "state -
of - the art" 700 series of new third generation underwater
epoxies.
3) Corro Coat
FC 2100 brushable, non hazmat epoxy coating with Dupont Kevlar
® and feldspar ceramic (also available in a cold water application
version, but this version is hazmat and cannot be shipped by air).
All are available for private labeling.
We also sell the original underwater
epoxy - putty like "Splash Zone®" epoxy.
Product sheets and MSDS at: www.epoxyproducts.com/datamsds.html
--
=======================================================
PAUL OMAN ----- Progressive Epoxy Polymers, Inc.
Frog Pond Hollow - 48 Wildwood Dr - Pittsfield NH 03263
10-4 Monday-Thur EST 603-435-7199 VISA/MC/Discover
info@epoxyproducts.com https://www.epoxyproducts.com
Boating site: https://www.epoxyproducts.com/marine.html
========================================================

|